How to Prepare for a Welding Inspection Milwaukee Professionals Recommend
How to Prepare for a Welding Inspection Milwaukee Professionals Recommend
Blog Article
Understanding the Value of Welding Evaluation in Ensuring Structural Stability and Safety And Security Throughout Various Industries
Welding assessment is an essential procedure that safeguards structural honesty and security across diverse sectors. As we discover the intricacies of welding assessment, the question occurs: what are the most critical elements that add to reliable assessment procedures?
Duty of Welding Evaluation
While the integrity of bonded structures is vital to security and efficiency, the function of welding inspection can not be overemphasized. Welding assessment acts as a critical quality assurance process that makes sure the adherence to established requirements and specifications throughout the welding procedure. By methodically evaluating welds for issues, disparities, and non-compliance, inspectors play a crucial duty in guarding the honesty of structures across different markets.
Welding examinations incorporate an array of activities, from pre-weld analyses to post-weld assessments. These evaluations not just identify prospective concerns prior to they intensify however also enhance the overall reliability and lifespan of bonded components. Welding Inspection Milwaukee. Evaluations aid to validate the ability and expertises of welders, making certain that welding procedures are carried out correctly and products are suitable
In addition, a strenuous assessment procedure cultivates compliance with governing requirements and industry criteria, decreasing the threat of catastrophic failures. By promoting a society of security and responsibility, welding assessment contributes considerably to both financial and functional performances. In sum, the function of welding examination is indispensable, as it underpins the quality, safety and security, and longevity of bonded frameworks necessary to modern facilities and market.
Kinds of Welding Examinations
Recognizing the various kinds of welding examinations is important for preserving the high quality and security of bonded structures. Welding examinations can be classified right into several kinds, each offering a details objective in the analysis process.
Visual evaluation is the most essential kind, involving a careful exam of the welds with the nude eye or through magnification. This method aids determine surface defects such as cracks, insufficient blend, or extreme spatter.
These techniques allow assessors to examine the stability of welds without compromising the material's framework. Ultrasonic screening uses high-frequency sound waves to identify interior defects, while radiographic testing employs X-rays or gamma rays to picture inner weld characteristics.
Destructive screening, though much less common, includes literally evaluating samples to recognize the weld's mechanical residential or commercial properties. Each type of assessment adds to an extensive evaluation, guaranteeing that welding meets sector criteria and safety demands.
Sector Requirements and Rules
Developing industry criteria and regulations is important for making certain the safety and integrity of welded structures. These criteria work as criteria for high quality, efficiency, and safety and security, assisting manufacturers and inspectors in the implementation of welding procedures. Numerous organizations, such as the American Welding Society (AWS) and the International Organization for Standardization (ISO), have actually established extensive requirements that determine treatments for welding practices, qualification of welders, and assessment strategies.
Conformity with these guidelines not just boosts the quality of welds but also reduces dangers related to architectural failings. Certain codes, such as the ASME Boiler and Pressure Vessel Code, outline demands for the building of pressure vessels, ensuring they can endure functional anxieties. Furthermore, national and local guidelines frequently mandate adherence to these industry standards, reinforcing their significance across industries like building and construction, aerospace, and automobile production.
Normal updates to these requirements reflect improvements in technology and welding strategies, ensuring that security procedures stay pertinent. Hence, a complete understanding and implementation of these standards is essential for welding experts, fostering a society of safety and security and top quality in welded structures.
Effects of Poor Inspections
Poor assessments can lead to severe repercussions in the welding industry, undermining the really criteria and policies made to guarantee safety and security and structural stability. The consequences of inadequate assessments can show up in numerous types, from instant security threats to lasting architectural failings.
Furthermore, inadequate examinations can stain a firm's credibility and result in legal repercussions, including penalties and lawsuits. Non-compliance with recognized criteria not just endangers the stability of projects but likewise diminishes customer count on the brand. Additionally, the financial ramifications can be shocking, encompassing both straight prices connected to repairs and indirect expenses such as important link shed company chances and increased insurance premiums. Inevitably, the ramifications of poor assessments prolong past specific tasks, influencing industry-wide criteria and public understanding, thus highlighting the vital need for effective and rigorous welding examinations.
Best Practices for Effective Assessments
Efficient welding assessments are extremely important to making certain the integrity and safety and security of welded structures. To achieve ideal results, examiners need to comply with numerous best methods that improve the inspection process.

Second of all, examiners should have the essential qualifications and qualifications relevant to the welding procedures and products being analyzed. Ongoing training and specialist growth are crucial to internet staying upgraded on industry standards and technological developments.
Additionally, utilizing suitable evaluation tools and strategies, such as visual assessments, ultrasonic testing, and radiographic analyses, is important for finding defects that could compromise structural stability.
Last but not least, extensive paperwork of the evaluation procedure is important. By implementing these best techniques, organizations can substantially boost the effectiveness of their welding evaluations and make certain safe, trusted procedures.
Final Thought
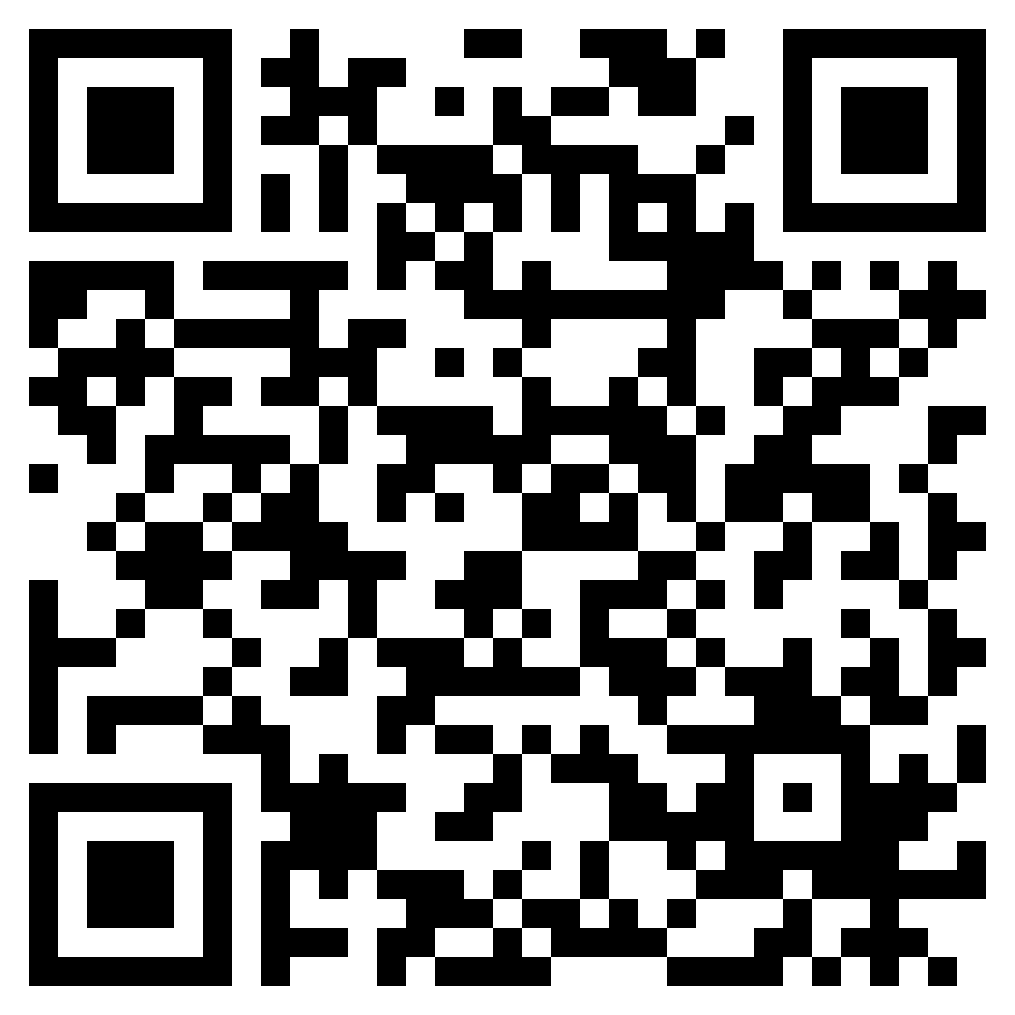
In conclusion, welding inspection is essential for keeping architectural stability and safety and security throughout numerous markets. Focusing on reliable welding evaluations is important to guarantee the safety of employees, properties, and overall functional integrity.
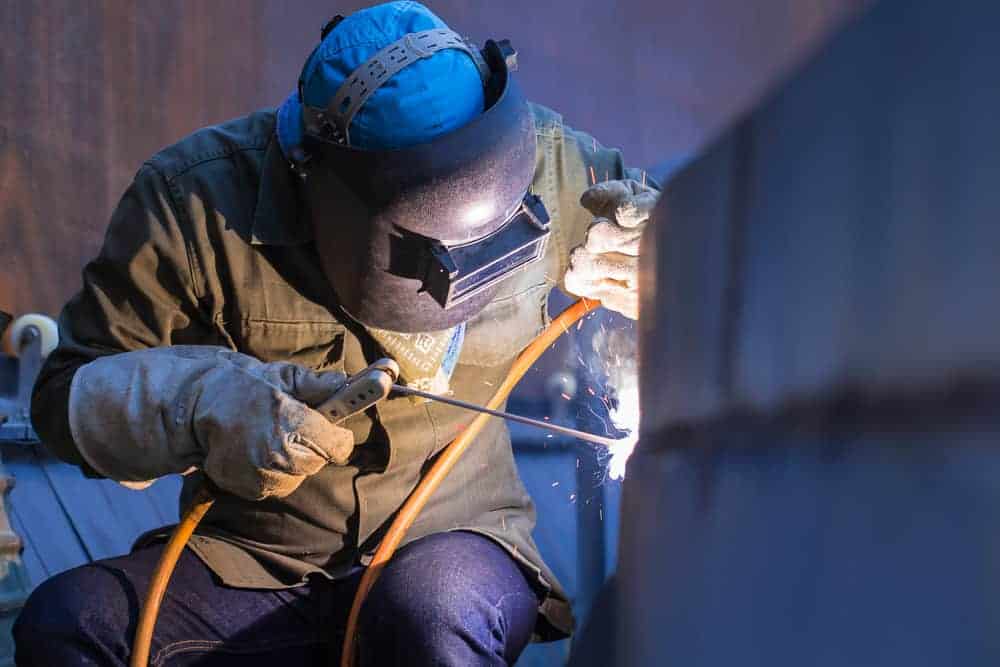
As we discover the complexities of welding examination, the concern develops: what are the most crucial elements that add to reliable assessment procedures?
Welding inspection offers as an essential top quality control procedure that makes certain the adherence to developed standards and specifications throughout the welding operation. In sum, the role of welding inspection is crucial, as it underpins the high quality, safety, and long life of welded structures necessary to modern-day framework and sector.
Numerous organizations, such as the American Welding Culture (AWS) and the International Organization for Standardization (ISO), have developed detailed requirements that original site determine treatments for welding methods, qualification of welders, and evaluation strategies.
Inevitably, the ramifications of poor assessments expand beyond specific tasks, impacting industry-wide requirements and public assumption, thus stressing the critical requirement for reliable and rigorous welding evaluations.
Report this page